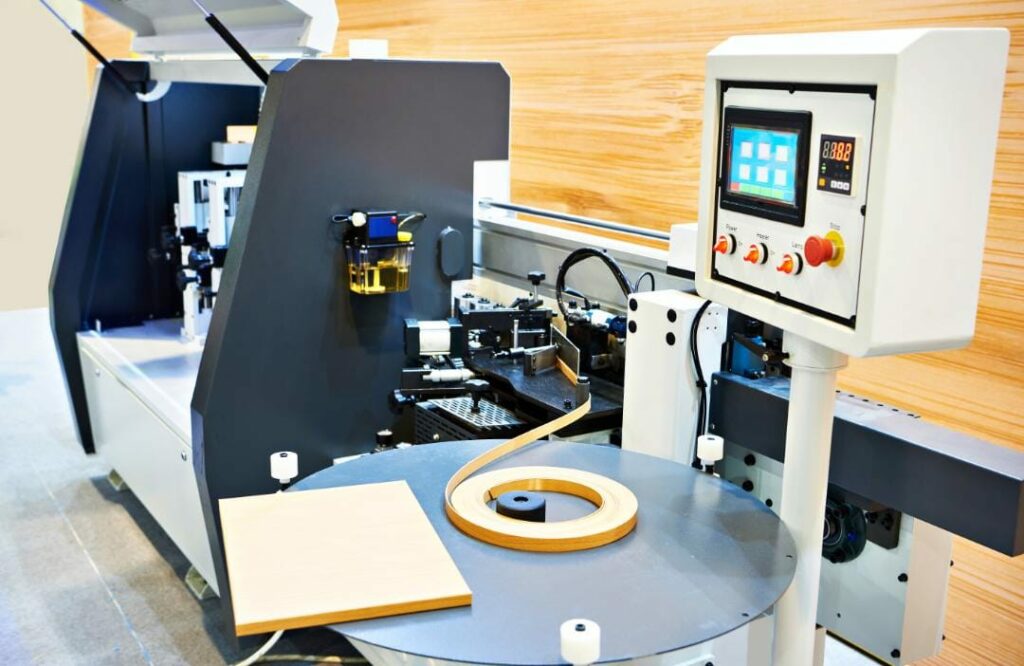
Introduction
Edgebanding is a critical process in woodworking, providing a polished finish and protective edge to the raw edges of panels and boards. Over the years, significant advancements in edgebanding equipment and edgebanders have transformed this process, enhancing efficiency, precision, and versatility. These innovations have not only elevated the quality of finished products but have also opened up new design possibilities for woodworkers and manufacturers.
Precision and Versatility in Edgebanders
Modern edgebanders are equipped with advanced technology that allows for unparalleled precision in edgeband application. High-frequency motors and laser-guided systems ensure that the edgeband is applied smoothly and accurately, even on intricate designs. This level of precision not only enhances the aesthetic appeal of the final product but also reduces the need for manual touch-ups.
Furthermore, edgebanders have become more versatile, accommodating a wider range of edgeband materials. Whether it’s PVC, ABS, wood, or acrylic, these machines can seamlessly apply different types of edgebands, allowing woodworkers to experiment with various finishes and textures.
Integration of Smart Technology
Advancements in edgebanding equipment have seen the integration of smart technology, which further optimizes the process. Edgebanders now come equipped with touch-screen interfaces and programmable logic controllers (PLCs) that allow for easy customization of settings. This means that woodworkers can fine-tune parameters like feed speed, glue application, and trimming, ensuring optimal results for each project.
Additionally, some edgebanders are now equipped with sensors that detect irregularities in the edgeband material or panel, automatically adjusting the application process to compensate for any discrepancies. This not only reduces waste but also minimizes the likelihood of errors in the final finish.
Enhanced Gluing Systems
One of the most critical aspects of edgebanding is the adhesive application. Recent advancements in gluing systems have led to the development of more efficient and precise glue application methods. Hot melt glue systems, in particular, have gained popularity for their quick curing time and strong bond.
Moreover, edgebanders now feature advanced glue pots and nozzles that ensure an even and consistent application of adhesive. This not only improves the overall quality of the finish but also minimizes excess glue, resulting in a cleaner workspace.
Compact and Space-Efficient Designs
Advancements in edgebanding equipment have also addressed the issue of space constraints in workshops. Manufacturers have developed compact and space-efficient edgebanders that maintain high levels of performance. These machines are designed to fit seamlessly into smaller workspaces without compromising on functionality.
Additionally, portable edgebanders have emerged, providing woodworkers with the flexibility to move the machine to different areas of the workshop or even on-site for on-demand edgebanding solutions.
Conclusion
The advancements in edgebanding equipment and edgebanders have revolutionized the woodworking industry, offering woodworkers a level of precision, versatility, and efficiency that was once unimaginable. With the integration of smart technology, enhanced gluing systems, and compact designs, edgebanding has become a streamlined process that significantly elevates the quality of finished products.
For woodworkers seeking the latest and most reliable edgebanding parts, Taurus Craco Machinery Inc. Parts & Supplies store is the go-to destination. With a comprehensive catalog of top-quality machinery and parts, they continue to lead the industry in providing woodworkers with the tools they need to achieve exceptional results.